Materials added to plastics to change their qualities are called fillers and additives. The two categories are inorganic and organic. Flame retardants lessen flammability, but organic additives like plasticizers boost flexibility and durability. Fillers and other inorganic additions improve mechanical strength. Antioxidants stop oxidative damage, whereas UV stabilisers shield against UV radiation. Plastics may be made more flexible, mechanically strong, resistant to flames, resistant to UV rays, and resistant to deterioration by using these chemicals. Follow us for more information.
An Introduction to Material Enhancement
Substances called fillers and additives are added to plastics to improve their performance and change their characteristics for certain uses. The inclusion of these chemicals can overcome or ameliorate some constraints that pure plastics may have, such as brittleness, hardness, combustibility, or excessive weight. The two main groups of additives are inorganic and organic. Carbon-based chemicals are the source of organic additives, while non-carbon-based materials make up inorganic additives. When added to plastics, both kinds of additives have distinct uses and advantages. It’s standard practice to alter the mechanical and physical characteristics of plastics with organic additions.
Plasticizers, for instance, are natural additives that give polymers more elasticity and toughness, increasing their resistance to breaking or splitting. By lowering the intermolecular forces that impede the movement of polymer chains, they are able to do this. As a result, the plastic becomes less brittle and more malleable. Flame retardants are another class of organic additives that are used in polymers to lessen their flammability. When these chemicals come into contact with heat or flames, they either release gases that restrict flame growth or create a coating of protective char. Flame retardants increase the safety and fire resistance of plastic products by reducing or stopping the spread of fire.
On the other hand, inorganic additives provide polymers with a variety of functions. Fillers are a typical inorganic addition that is used to increase the mechanical strength of polymers. Typically, fillers are added to the plastic matrix as solid particles, including glass fibres or mineral powders. They improve the plastic’s dimensional stability, stiffness, and resistance to impact, increasing its strength and suitability for structural uses.
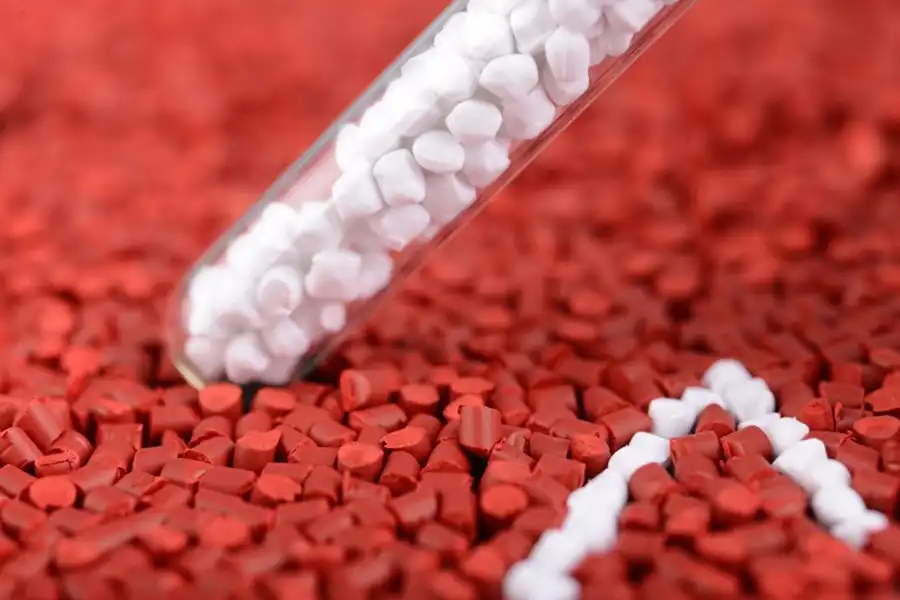
Read more: What is DOP?
Understanding the Building Blocks: The Essence of Fillers
Fillers are a vital part of many materials and are responsible for improving their qualities. Fillers are solid particles mixed into the plastic matrix in the context of plastics. They function as an essential component, adding to the material’s overall qualities and performance. Fillers are primarily used in plastics to enhance their mechanical qualities. Fillers can be included in the plastic matrix to create a number of desired effects. Enhanced rigidity and strength are the two main advantages. Fillers serve as reinforcements, strengthening the polymer chains and giving the plastic its structural integrity. This leads to increased dimensional stability, greater deformation resistance, and increased load or stress tolerance. Furthermore, fillers can increase the plastic’s resilience to impact, preventing it from shattering or splitting. Fillers lessen the chance of brittle failure by helping to distribute and absorb energy.
Mineral Fillers: Harnessing the Power of Earth’s Resources
When it comes to asphalt mixes, mineral fillers are crucial in improving the mixture’s overall characteristics and performance. During the manufacturing process, finely ground inert mineral elements are added to the asphalt mix to create mineral fillers. Increasing the mixture’s density and strength is one of the main goals of adding mineral fillers to asphalt mixtures. By filling the spaces created by the bigger aggregates, the filler’s small particles improve the compactness and decrease the permeability of the asphalt mix.
This results in increased resilience to moisture infiltration and durability, both of which can help the pavement last longer. Additionally, mineral fillers enhance the asphalt mixture’s overall strength. They enhance the mix’s binding and interlocking properties by filling the voids left by the bigger aggregate particles. The pavement’s cohesiveness, stability, and load-bearing capabilities all rise as a consequence. By distributing stresses more uniformly throughout the mixture, fillers lessen the likelihood of cracking or rutting when subjected to high traffic loads.

Polymeric Fillers: Transforming Materials with Polymers
Enhancing the material’s mechanical qualities is one of the main goals of utilising polymeric fillers. The fillers strengthen the structure of the composite material by adding polymers into the matrix, which increases the material’s strength, toughness, and impact resistance. The polymers diffuse throughout the matrix and serve as a reinforcing phase, adding more stiffness and strength. The material’s overall durability, resistance to deformation, and load-bearing capability may all be enhanced by this reinforcing effect. Moreover, polymeric fillers can improve the host material’s other useful qualities.
For instance, by adding flame-retardant polymers, they can increase thermal stability and flame resistance. When exposed to heat or flames, these fillers release gases or create a protective char layer that increases the material’s fire resistance while decreasing its flammability. Polymeric fillers can also change a material’s electrical and thermal conductivity. In order to improve the material’s conductivity to heat or electricity, the fillers can incorporate conductive polymers or polymer composites into the matrix. This is especially helpful in situations where thermal or electrical conductivity is needed, as in heat dissipation systems or electronic gadgets.
Inorganic Fillers: Exploring the Inorganic World of Material Enhancement
Inorganic fillers are solid particles that are added to a matrix material to modify properties such as strength, stiffness, and thermal conductivity. Common types of inorganic fillers are silica, calcium carbonate, glass fibres, carbon black, alumina, talc, and barium sulphate. The advantages of using inorganic fillers include reinforcement, improved thermal conductivity, cost reduction, dimensional stability, and enhanced chemical resistance. Processing conditions, dispersion, compatibility, and filler loading are challenges that must be carefully considered for the best results.
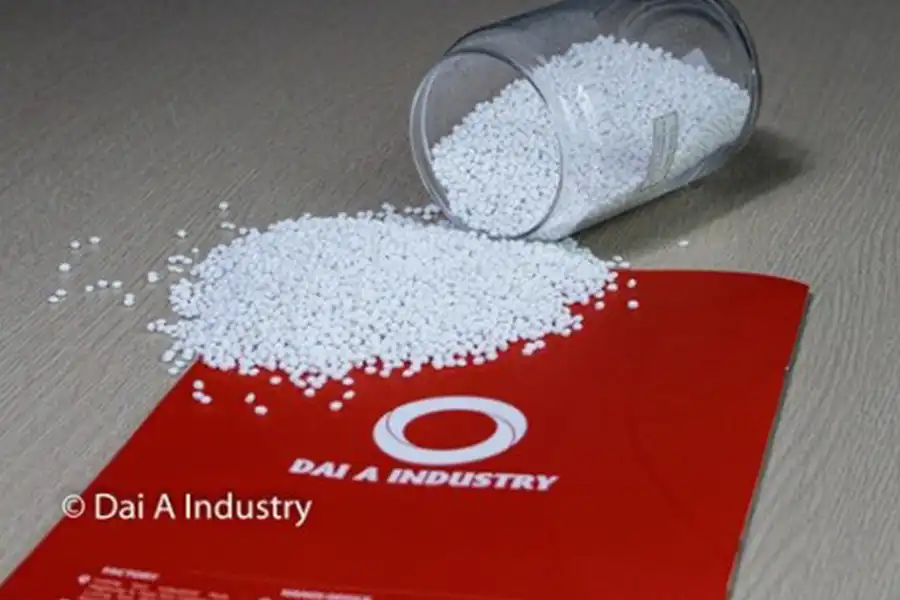
From Plastics to Construction: Common Applications of Fillers
Fillers are widely used to improve the characteristics and performance of materials in sectors such as building and plastics. Typical uses are as follows:
۱٫ Plastics: In thermosetting plastics, PVC formulations, and polypropylene and polyethylene compounds, fillers enhance stiffness, impact resistance, and dimensional stability.
۲٫ Construction: In concrete, mortar, plaster, plasterboard, sealants, and adhesives, fillers improve strength, durability, workability, and fire resistance.
۳٫ Additional uses: Fillers strengthen rubber goods, increase strength and thermal characteristics in the production of ceramics and glass, and improve opacity, scratch resistance, and corrosion resistance in paints and coatings.
Fillers are essential for modifying the characteristics of materials, enhancing their performance, and extending their range of applications.
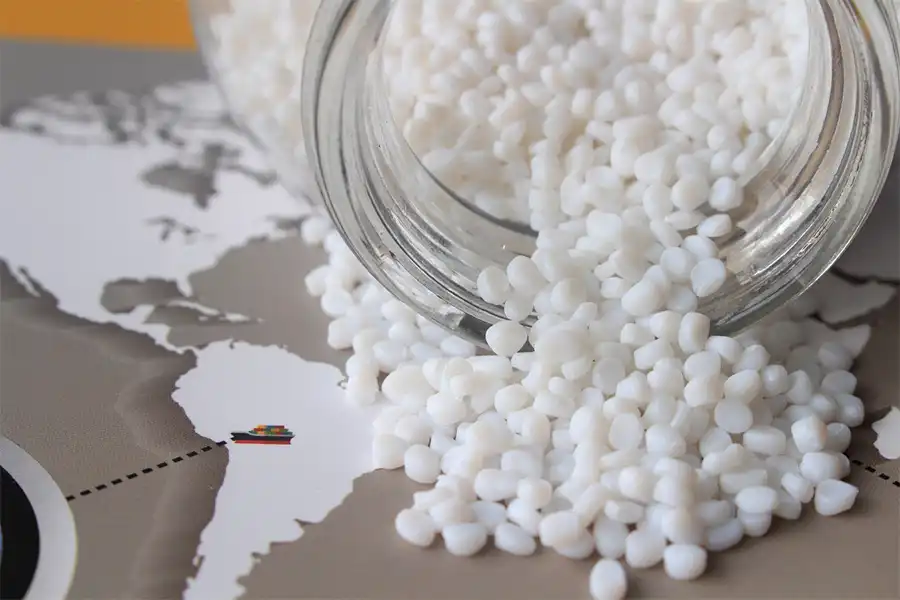
Read more: Hoses
Beyond the Surface: How Fillers Influence Material Properties
Fillers have a big impact on material qualities that go beyond the surface. Fillers can be used to change the mechanical, thermal, electrical, and other characteristics of a variety of materials. Let’s see how fillers affect the characteristics of materials:
Reinforcement
Fillers can improve a material’s stiffness, strength, and ability to withstand impacts. They strengthen the material’s structural integrity and load-bearing capability by acting as reinforcing agents. Toughness: Materials can be made more resilient to cracking and fracturing by adding fillers, such as rubber particles or elastomeric fillers, which improve the materials’ energy absorption capacity. Wear Resistance: Materials can be made more wear-resistant by adding fillers such as glass fibres, carbon black, or ceramic particles, which can lessen surface damage and increase material longevity.
Properties of heat
Thermal Conductivity: High thermal conductivity fillers, such as boron nitride or alumina, can improve a material’s capacity to transport heat. In situations where effective heat control is necessary, this feature is essential. Thermal Expansion: Fillers can affect a material’s coefficient of thermal expansion, which can minimise the chance of warping or distortion and lessen dimensional changes brought on by temperature fluctuations.
Electrical Properties: Materials’ electrical conductivity may be increased by adding certain fillers, such as metallic or carbon black particles. When electrical conductivity or static dissipation are necessary, this feature is crucial. Dielectric Properties: Fillers can alter a material’s dielectric strength and dielectric constant, which can have an impact on how electrically insulated it is.
Additional Features
Fillers can improve a material’s barrier qualities, such as its resistance to moisture or gas permeability, which qualifies it for protective or packaging uses. Flame Retardancy: Certain fillers, such as magnesium hydroxide or aluminium hydroxide, can make materials more flame-retardant, which lowers their flammability and increases safety. It is noteworthy that the final material qualities can be greatly influenced by the kind, amount, and compatibility of fillers in relation to the matrix material. To obtain the needed improvements in particular applications, filler-matrix combinations must be carefully chosen and optimised.

Manufacturing Magic: The Art of Incorporating Fillers
Fillers must be manufactured carefully, with an emphasis on uniform distribution and benefit maximisation. Filler loading, processing conditions, mixing and dispersion, compatibility, quality control, and filler selection are important factors. Manufacturers are able to produce materials with certain qualities by optimising these elements. The skill is striking a balance between the required material performance and the addition of filler.
As the top producer of plastic materials in Iran, karachemicals is active in the field of producing products such as EVA granules and PVC with the help of advanced machines and sends its products all over the world. For the bulk purchase of all kinds of granules, it is enough to contact the experts of this company through our contact page. We are available to you every day of the week.
Fillers have a big influence on a material’s characteristics. They can change the material’s density and improve mechanical strength, hardness, dimensional stability, electrical conductivity, and thermal conductivity. Properties including flexibility, chemical resistance, flame retardancy, and impact resistance can also be impacted by fillers.
Rubber, plastics, paints and coatings, adhesives and sealants, building supplies, paper, cosmetics and personal hygiene goods, and the food and beverage sector are just a few of the industries that frequently employ fillers. In the appropriate applications, they enhance qualities including workability, texture, bonding strength, opacity, viscosity, and mechanical strength.
Better mechanical qualities, lower costs, more dimensional stability, longer durability, a better appearance, stronger chemical resistance, greater thermal and electrical conductivity, and easier process ability are all advantages of employing fillers in manufacturing processes.
2 thoughts on “what are Fillers? Everything You Need To Know”